

- #Add file to sinutrain manual
- #Add file to sinutrain full
- #Add file to sinutrain software
- #Add file to sinutrain plus
It is commonly known in the trade as 3+2 programming. The high-speed machining feature is highlighted here by Cycle 800, which is a static plane transformation that allows a 5-axis machine to define a rotated working plane in space. The procedure can also be automated to run on the table at prescribed time intervals.” As Siemens technical applications center manager Randy Pearson observes, “This feature is a huge time saver for our customer, as the test ball and probe in the spindle mechanism can be run at any point in the cycle, testing the actual machine kinematics at any time. The 3D quick set compressor feature provides a parametric itemized data file for all path motions, thereby eliminating collision and ensuring the optimum tool path, in conjunction with the NC kernel and PLC on the machine tool. Once the program was ready for the CNC, the features of that control allowed a more streamlined simulation of the actual cutting path. Both high-speed roughing and precise 5-axis machining are possible on this small footprint, entry-level machine.
#Add file to sinutrain manual
This avoids manual programming and, as a result, reduced the program transition time from as long as two days to approximately 30 minutes.Īn oil field rock bit being machined on a DMU 50 with Siemens 840D sl CNC. The User Defined Events (UDEs) feature inside the NX program allows simple check boxes for triggering post-processors references for coolant pressure, spindle speed settings and more.
#Add file to sinutrain full
Starting from the CAD file, the Siemens PLM team ran the program through its NX CAM process, eliminating the set-ups through full 5-axis operation. This scenario was particularly applicable in this case, as the production runs were anticipated to be low with short lead times.

#Add file to sinutrain software
By offering a total package of CAD-CAM-CNC hardware, software and engineering services, Siemens was able to help the machine builder substantially improve every aspect of part production, including reduction of design-to-part protocols, machining time, tool life, surface finish, dimensional accuracies and overall production efficiencies. The machine builder turned to its longtime business partner, Siemens, for assistance.
#Add file to sinutrain plus
Both high-speed roughing and then very precise 5-axis machining were required in this small footprint machine, which had been selected by the customer due to specific plant capacity utilization concerns, plus their desire for a flexible, reasonably priced and highly cost-effective machine tool.Ĭlose up of the DMU 50 with Siemens’ 840D sl CNC. The customer, a major upstream oil industry supplier, was trying to decide if the better path for this product was a single block of steel or a near net casting being machined. The customer further presented the builder with the need for fast changeover to produce the part from various metal materials, with all the attendant tool changes and workpiece setup variances present. On one recent application, DMG MORI was challenged with a 440-pound, 8” diameter x 8” high workpiece made from 1045 grade steel and being machined into a rock bit for oil field exploration.
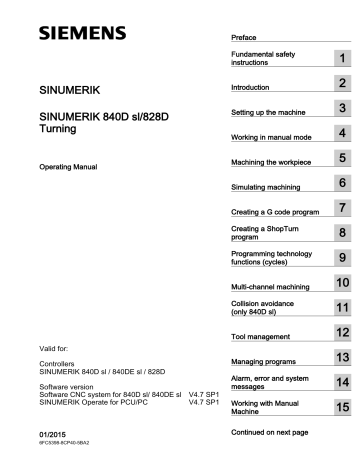
“It is a David handles Goliath type of story,” says Matthias Leinberger, the business development director for Siemens PLM (Product Lifecycle Management).
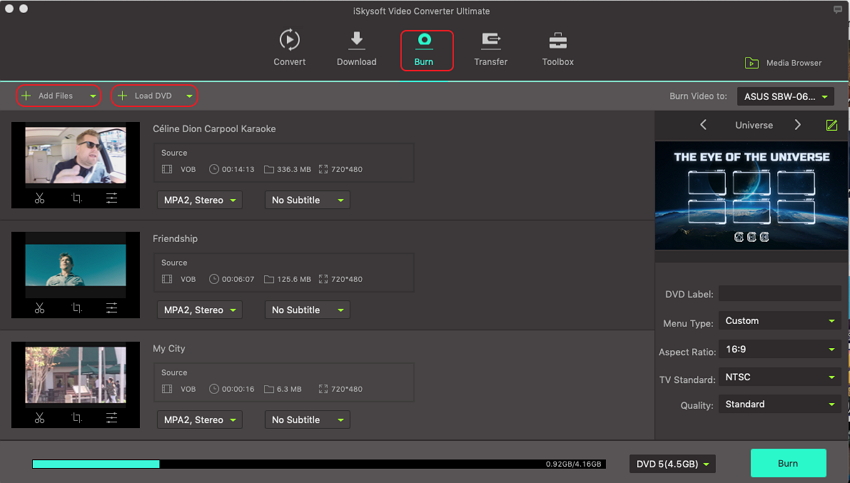
The DMU 50, although an entry-level 5-axis machining center from DMG MORI, is a compact unit that features considerable strength, as the following example will detail. Typically, components produced for the oil-and-gas field are very large, very heavy and often have complex contours, making the machining time long and the tool life short. Inherent in this market are several factors that lobby for great care and planning in the machining process. The features of the 840D allow a streamlined simulation of the actual cutting path.ĭMG MORI manufactures a wide variety of conventional chip-cutting machining centers for OEMs and production job shops serving the demanding oil-and-gas industry. A DMG employee showcasing the DMU 50 with Siemens’ 840D sl CNC.
